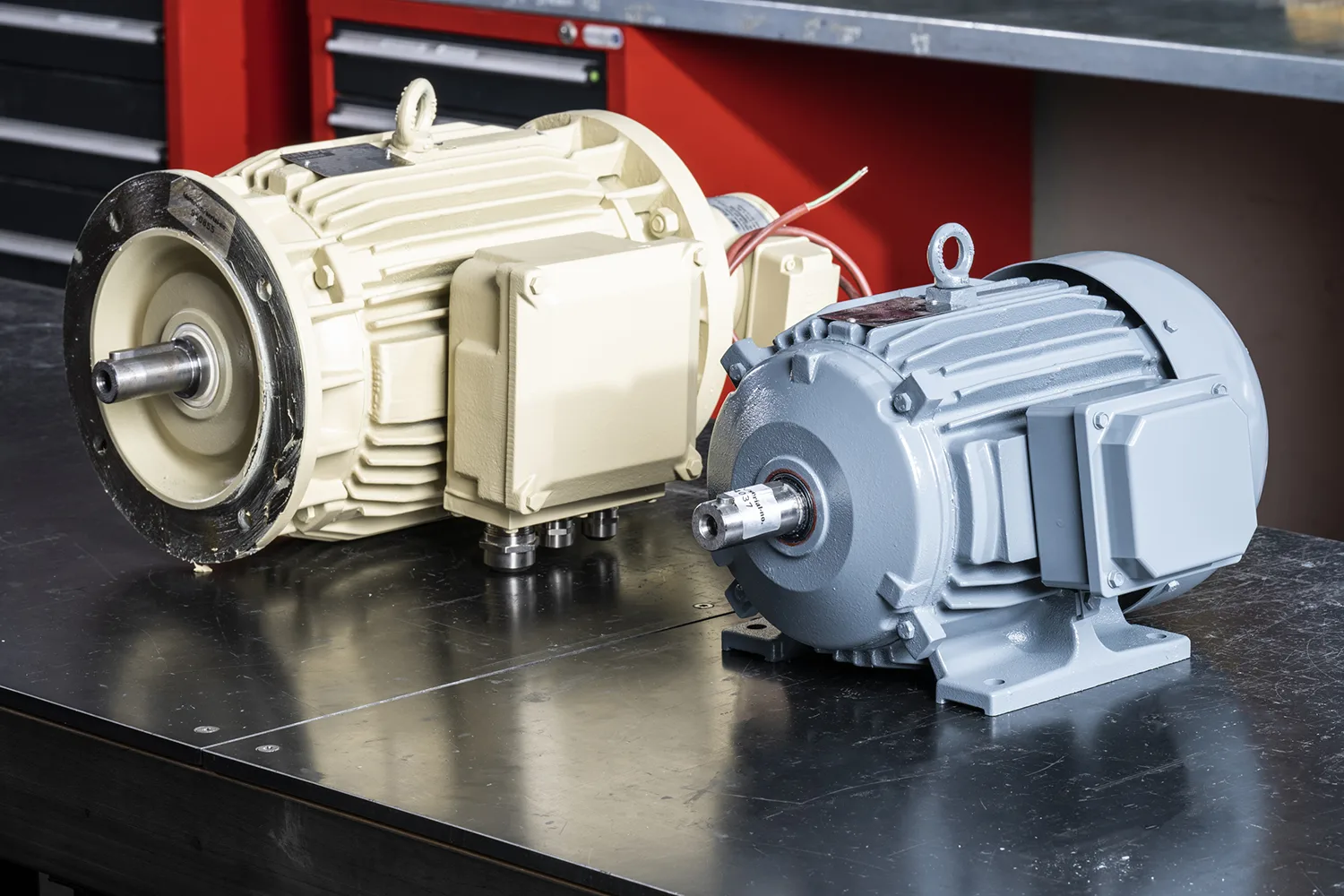
Dust can spell danger. That’s because the occurrence of gases or dust during the processing of materials and substances can lead to an explosive atmosphere. Our recently certified dust- and explosion-proof motors are engineered for use in such settings.
An explosive atmosphere can occur in many different applications and in many different sectors, like the food industry, animal feed processing, the chemical and pharmaceutical industries or recycling. That’s why avoiding sparks and heat in the immediate vicinity is an absolute must. Our tKD..71..-./. to tKD..315..-./. motor series was recently certified as dust-proof and explosion-proof in accordance with IBExU22ATEX1087 X for such applications. Thanks to our many years of experience in the offshore sector with explosion-proof and waterproof motors for winch drives and a host of other uses, adapting the design for dust-protected motors was a piece of cake.
Application example: sugar mills
Because they are used in systems for grinding material, such as at flour or sugarcane mills in the food industry, such motors have to be dust- and explosion-proof to ensure safety. The finer the material, the easier it is for a deflagration to occur if dust combusts due to sparks or high surface temperatures in the environment. That kind of situation can occur when grinding coarse sugar into powdered sugar, for example.
In such a system, the coarse sugar is fed into the grinding zone through a filling pipe, where it comes into contact with pin discs that grind the material finer and finer. The more discs and pins are used within these discs, the finer the sugar becomes. The motor is located outside the actual working area to prevent the sugar and any dust from coming into contact with the motor during the grinding process. However, if the grinding area is later opened for maintenance, cleaning or other procedures, there may be residual dust that could ignite if the motor surface is too hot.
Active temperature monitoring
Our customers specify the critical ignition temperature for the desired application. We design our motors accordingly for the application in question. At sugarcane mills, for instance, the surface temperature of the motor must not exceed 200 degrees Celsius. Thanks to customisable, integrated, active temperature management, our motors are engineered to prevent this level from being reached in the first place. One option is a thermal sensor, which would switch off the motor if the winding overheats. Alternatively, an overcurrent cut-off device can be installed, which also deactivates the motor in the event of an overload.
Engineered for animal feed, chemicals, pharmaceuticals and the recycling industry – even as a retrofit
Dust-proof, explosion-proof motors can also be used in the crushing of animal feed or in the chemical and pharmaceutical industries to help make colour pigments for powder coatings and paints, as well as in a host of other applications. Since the separation, filtering and shredding of recycling material can generate potentially explosive dust, recycling facilities are another environment where such motors can come in handy.
The certified motors offer benefits for new and old systems alike. Especially in existing systems, stricter regulations on certain hazardous materials and working environments may make it necessary to replace motors. Higher efficiency standards can also be a reason to replace a motor. Increasing efficiency by 1% or 2%, as with the use of our motors, can result in significant energy cost savings.
In retrofit projects like these, we customise our motors to match the conditions and installation situation on site – in line with the manufacturing philosophy that makes our company special.